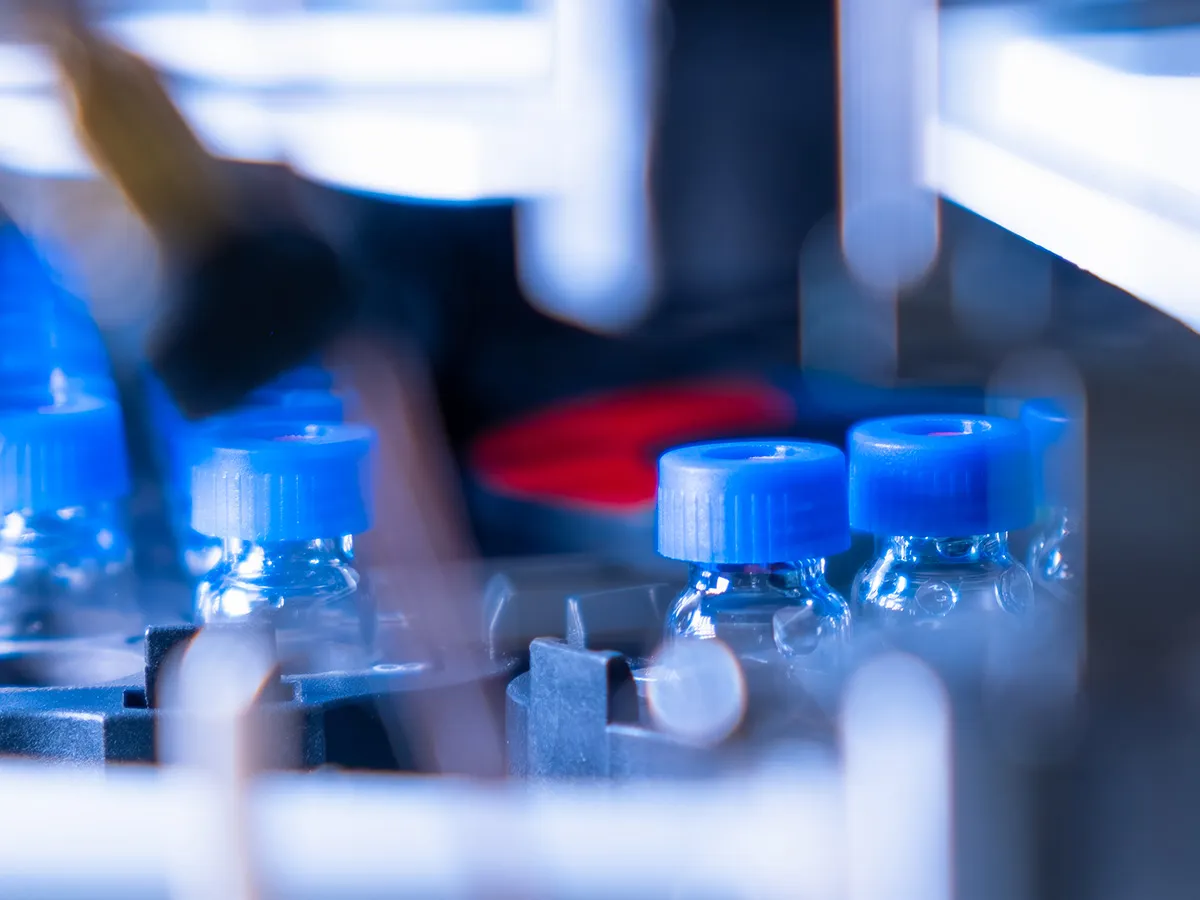
In any controlled environment avoid equipment off-cycles so you don’t “lose the room!”
In any controlled environment avoid equipment off-cycles so you don’t “lose the room!” Maintaining tight temperature and humidity levels in controlled environments such as cleanrooms is critical to prevent material damage, production loss, and shutdowns. Installing the Rawal Devices’ APR Control can be the perfect, cost-effective solution to avoid any interruptions in production as a result of the failure to maintain quality.
Here’s How to Achieve Optimal HVAC Performance for Cleanroom Environments
Cleanrooms exist in an abundance of industries where sensitive materials are involved in the manufacturing process. Controlling temperature and humidity within a narrow range is critical to prevent any airborne particle contamination, including condensation and bacterial growth. Even with sophisticated HVAC systems and complex controls, it can be almost impossible to maintain these ideal conditions. Rapid cycling of the compressor is inevitable as these high-end HVAC systems simply can’t react to the changing environment fast enough to provide sufficient dehumidification. The addition of the APR Control to a standard new unit or an existing system will prevent or eliminate cycling to keep the space within design specifications, and within regulatory compliance.
Cleanrooms have different classifications that require different temperature and humidity levels. Some cleanrooms require the temperature to be maintained at 68°F (+/- 1°F) with a relative humidity of 55%RH (+/- 5%RH). In addition to these tight tolerances, many cleanrooms are required to maintain higher-than-normal Air Changes Per Hour (ACPH) to prevent contamination.
For example, a conventional building (Office/retail space) could have as little as 6 ACPH. Hourly air changes for cleanrooms applications such as pharmaceutical, packaging and manufacturing, and biosciences are much more stringent. These classes of cleanrooms could be required to have upwards of 30 ACPH depending on the class of the cleanroom to maintain exceptional air quality. The top classes of cleanrooms where sensitive processes are performed have the strictest cleanroom classifications. In applications such as microelectronics or sensor manufacturing, we’ve seen as high as 500 ACPH for such environments with strict air quality control and consistent removal of contamination.
Having more air changes in cleanrooms only amplifies the need for consistent discharge air temperatures. As more outdoor air may be introduced, even the shortest of system off times can quickly bring the room out of design & operational specifications; risking “Losing the Room!” The APR Control provides capacity modulation to match the changing load of the return/outdoor (fresh) air entering the evaporator. As a result, the APR can eliminate cycling and keep the coil (below dewpoint for continuous dehumidification while) in a constant state of cooling to remain within spec to avoid “losing the room!”
The APR Control has been successfully installed in labs, hospitals, and cleanrooms with under-performing systems to improve functional capabilities and maintain tight temperature and humidity requirements.
Case Studies
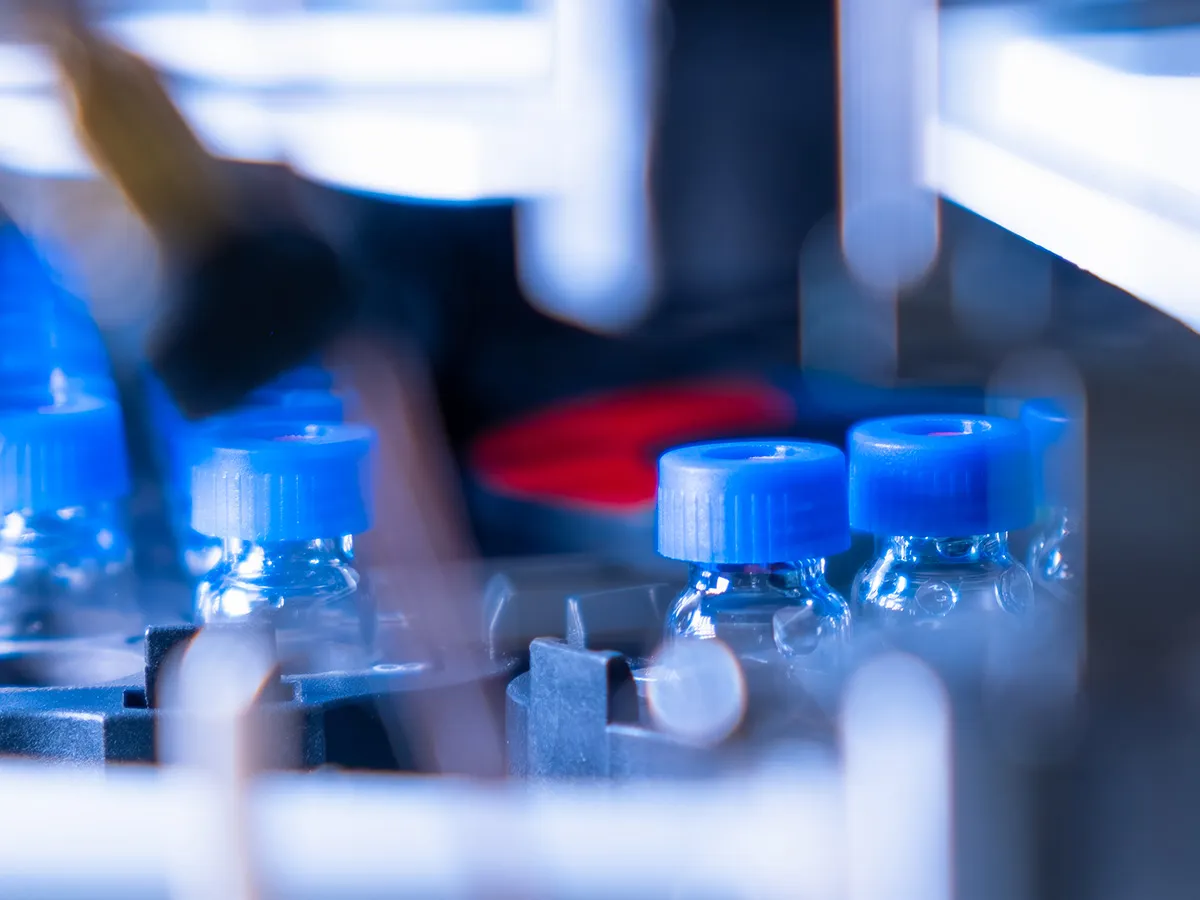